Manufacturing
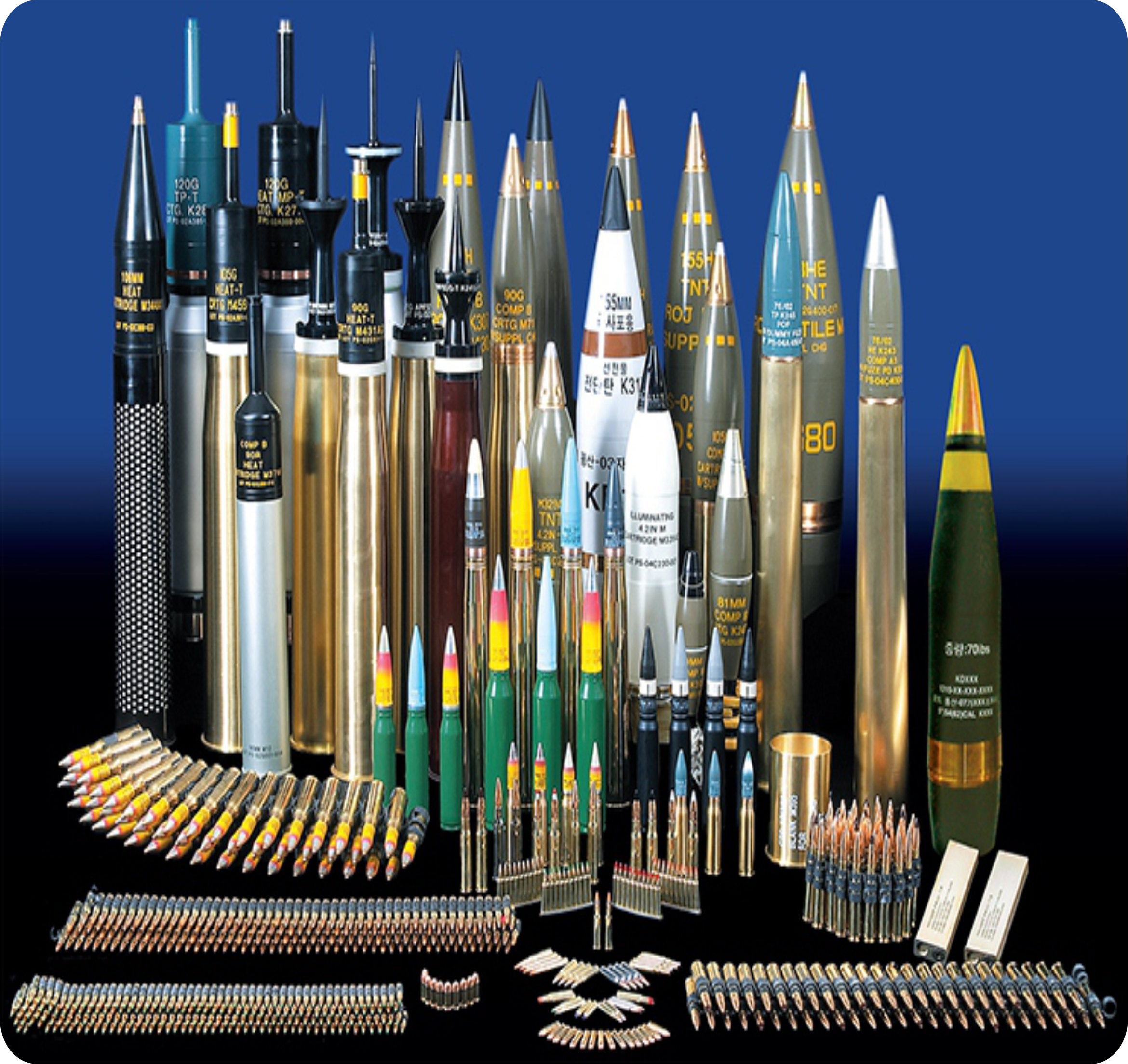
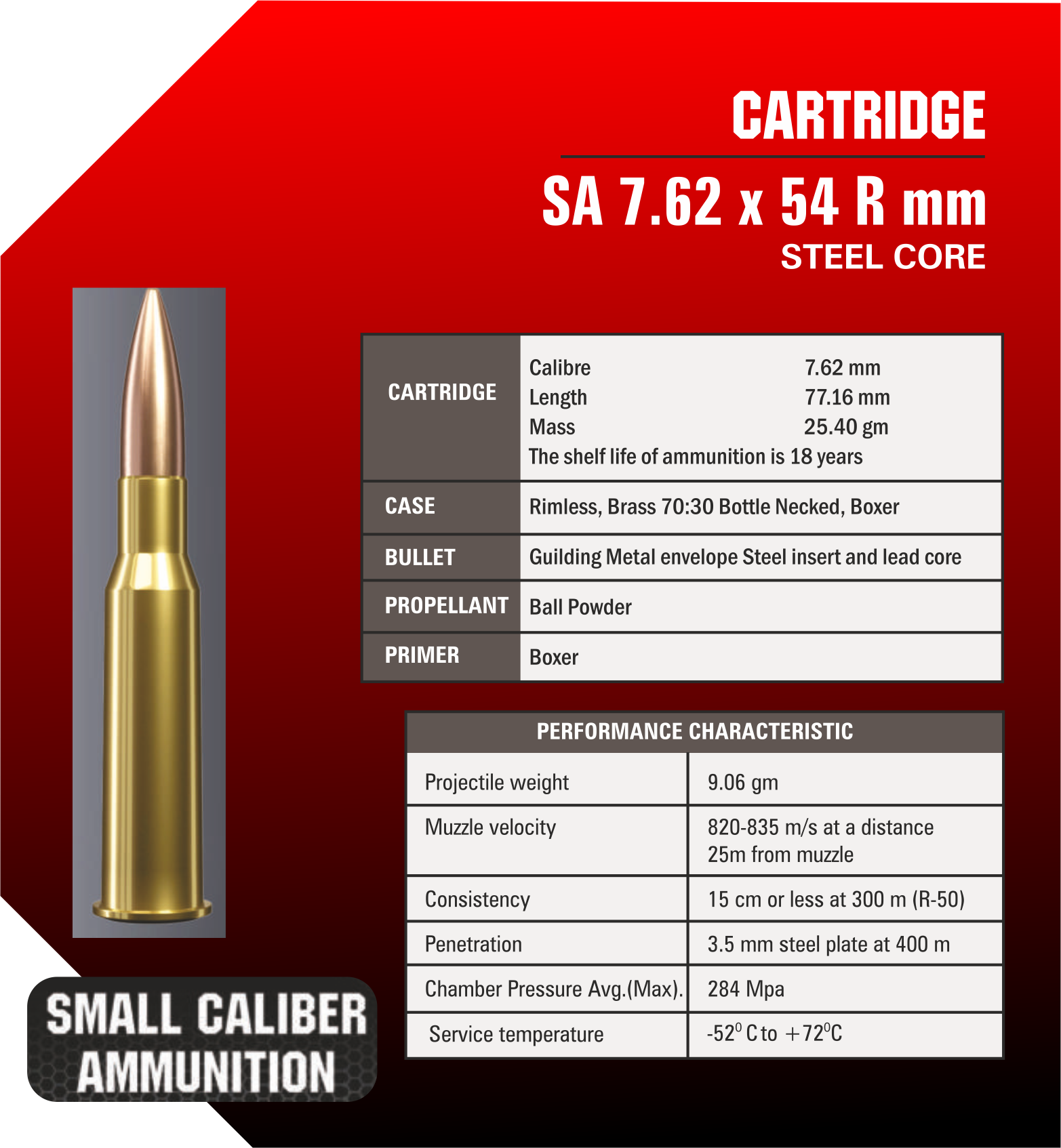
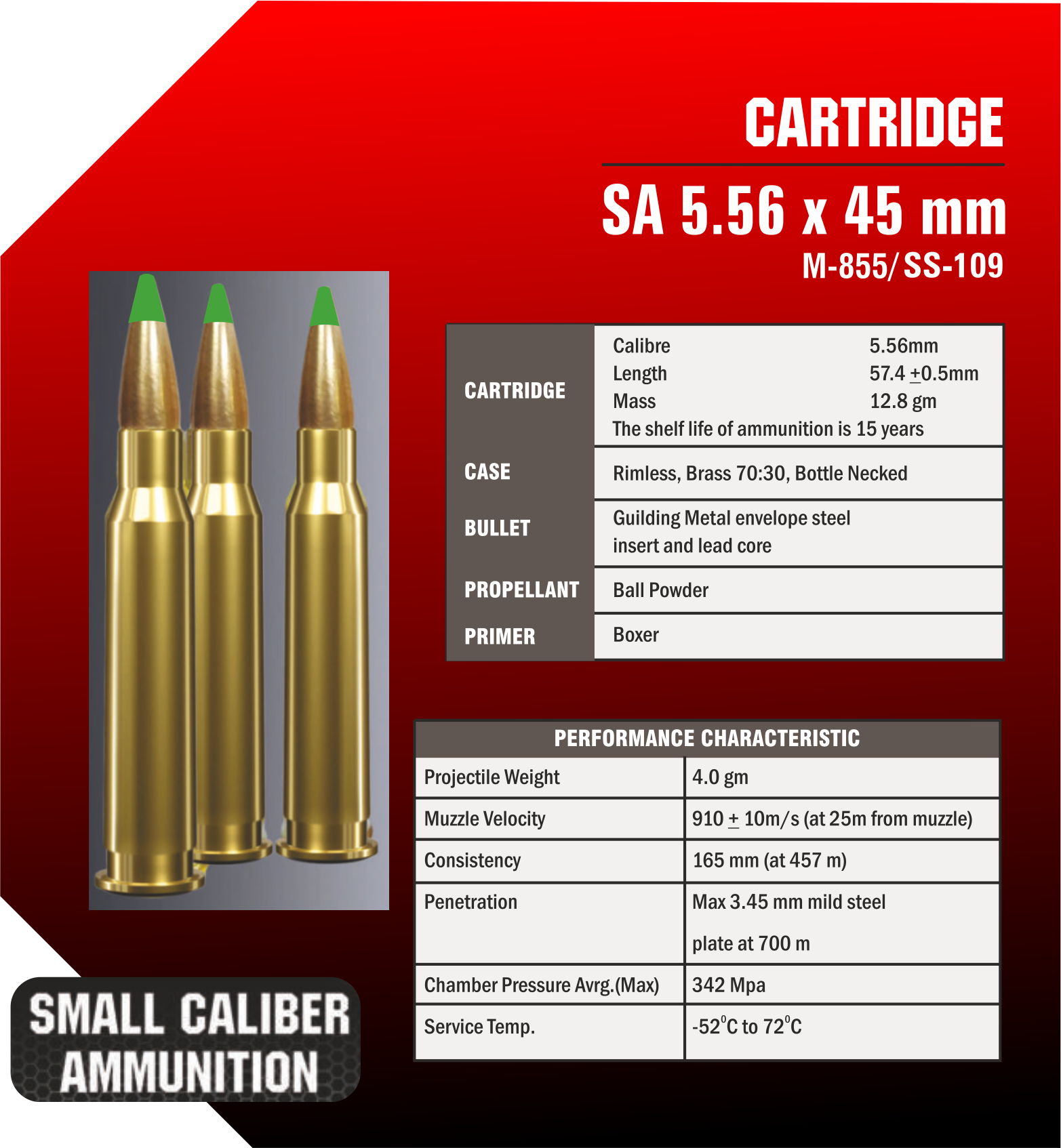
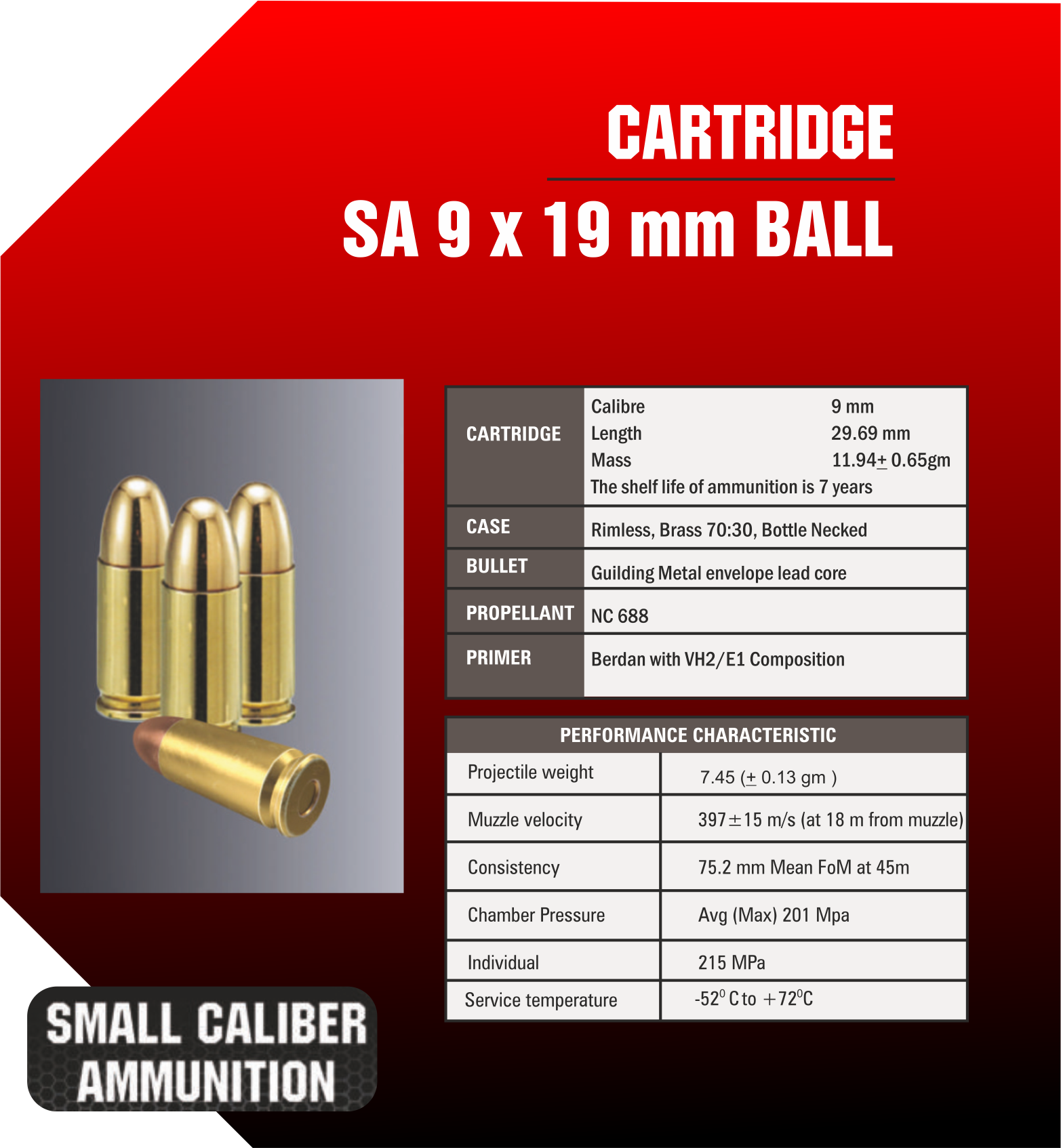
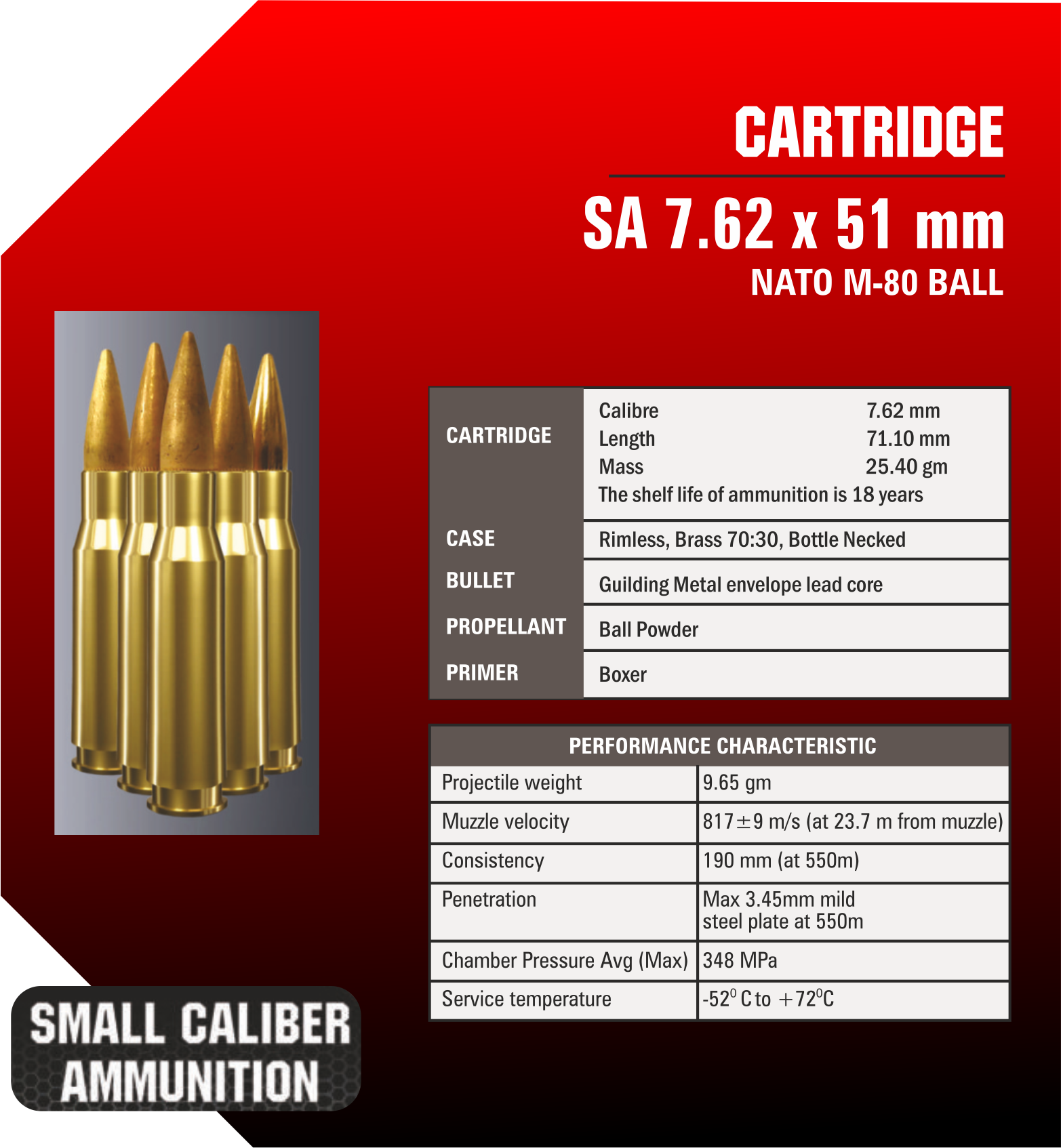
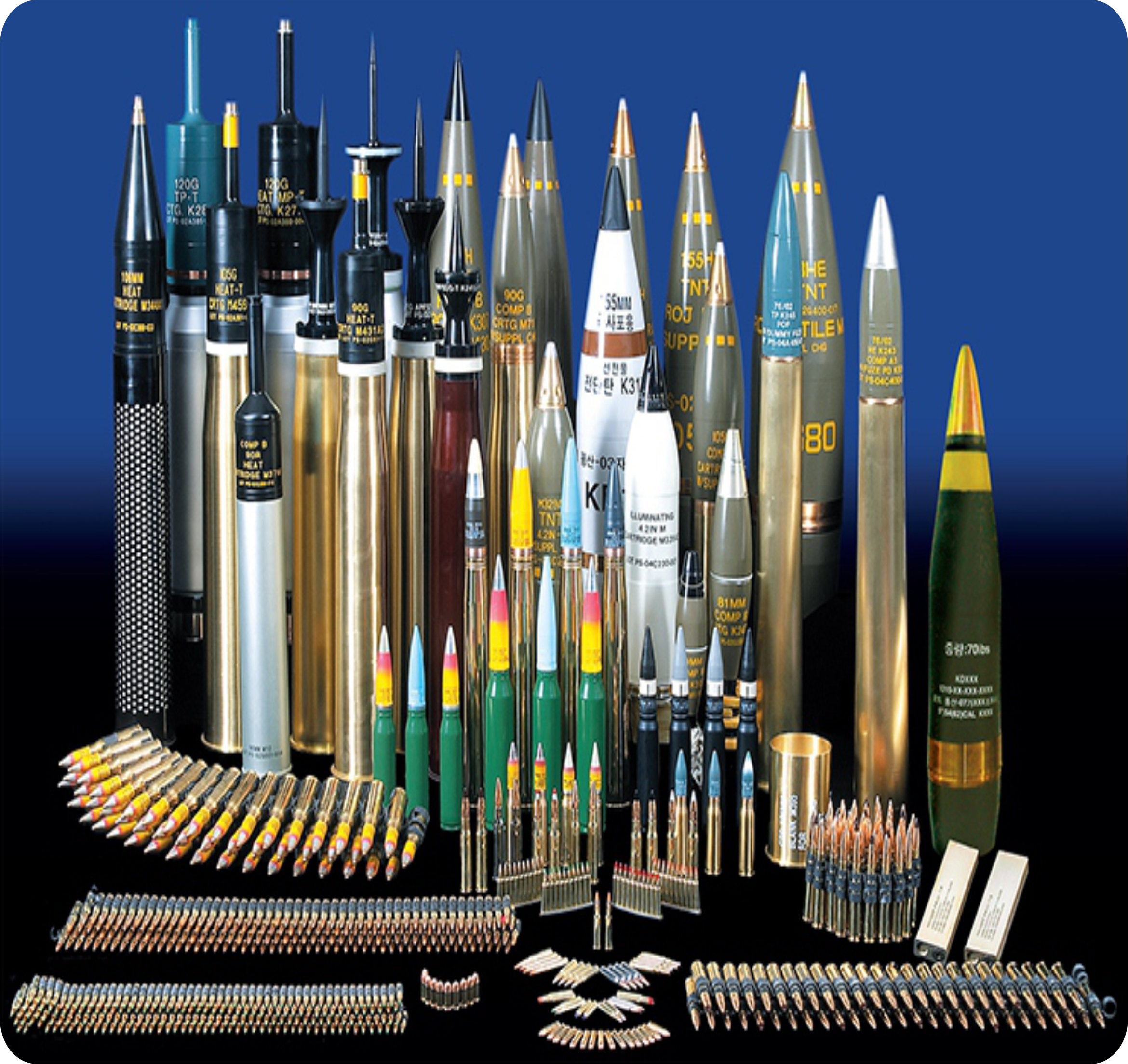
Manufacturing 155 mm Shell Casings
Manufacturing 155 mm shell casings involves producing the outer metal shells that encase the explosive components and propellant of artillery rounds. These casings are critical for the functioning of artillery ammunition and must meet stringent standards for safety, durability, and precision. This guide covers the essential aspects of manufacturing 155 mm shell casings, including processes, materials, and considerations.
1. Components and Specifications
*Shell Casing*: The outer structure that houses the projectile and other internal components. It is typically made from high-strength brass or steel.
– *Specifications*: Must meet precise dimensions and tolerances to ensure compatibility with artillery systems and reliable performance.
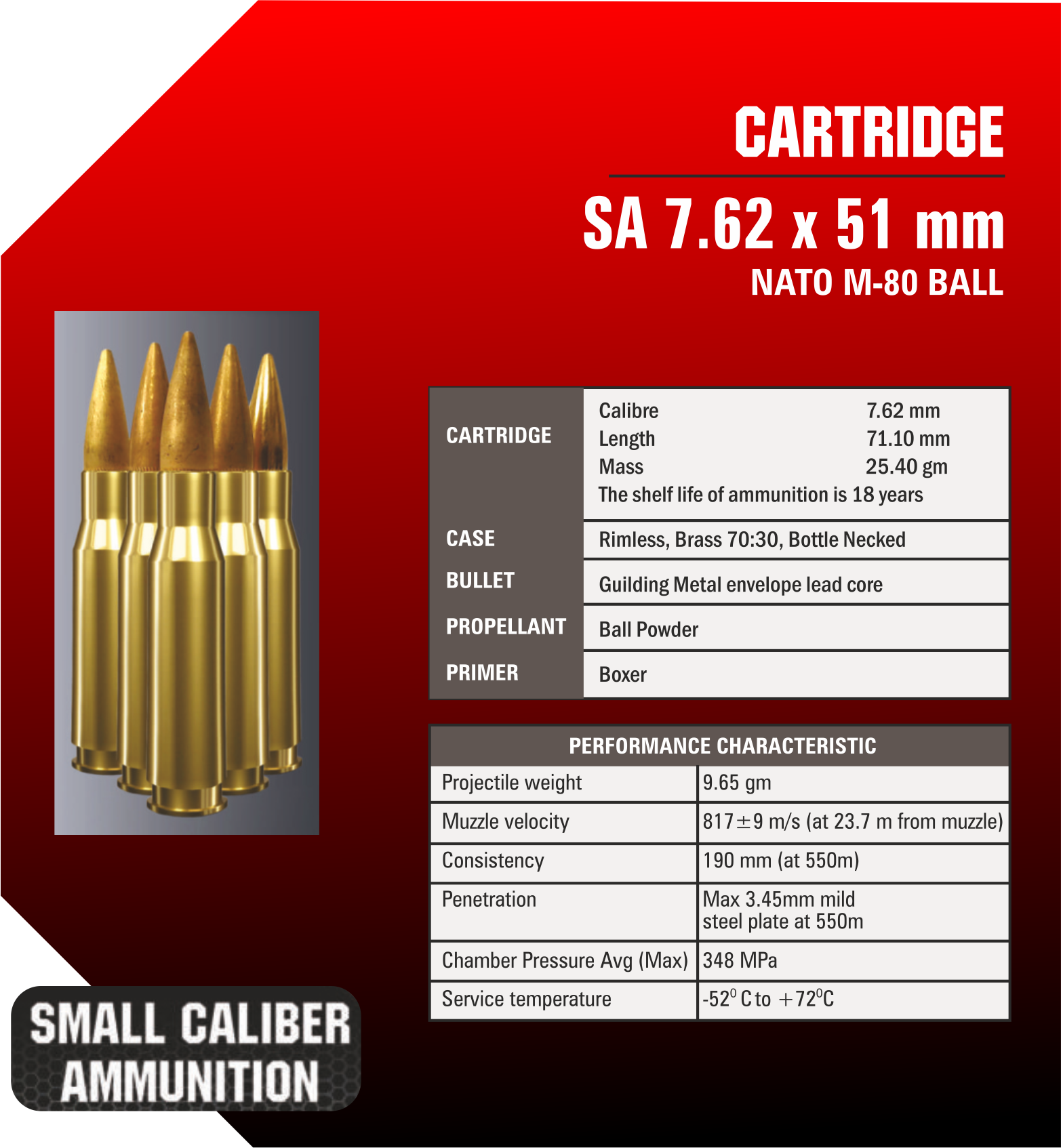
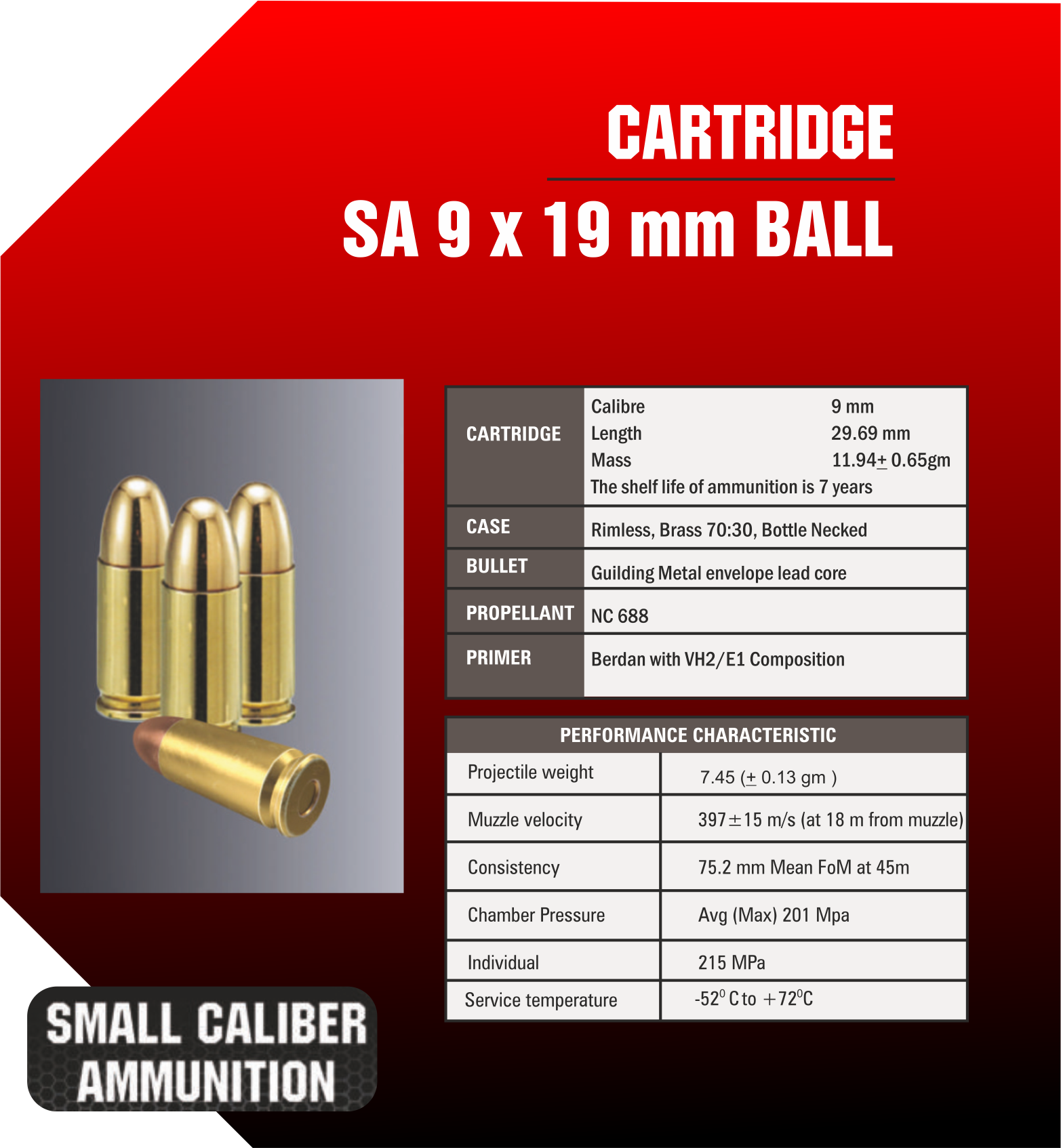
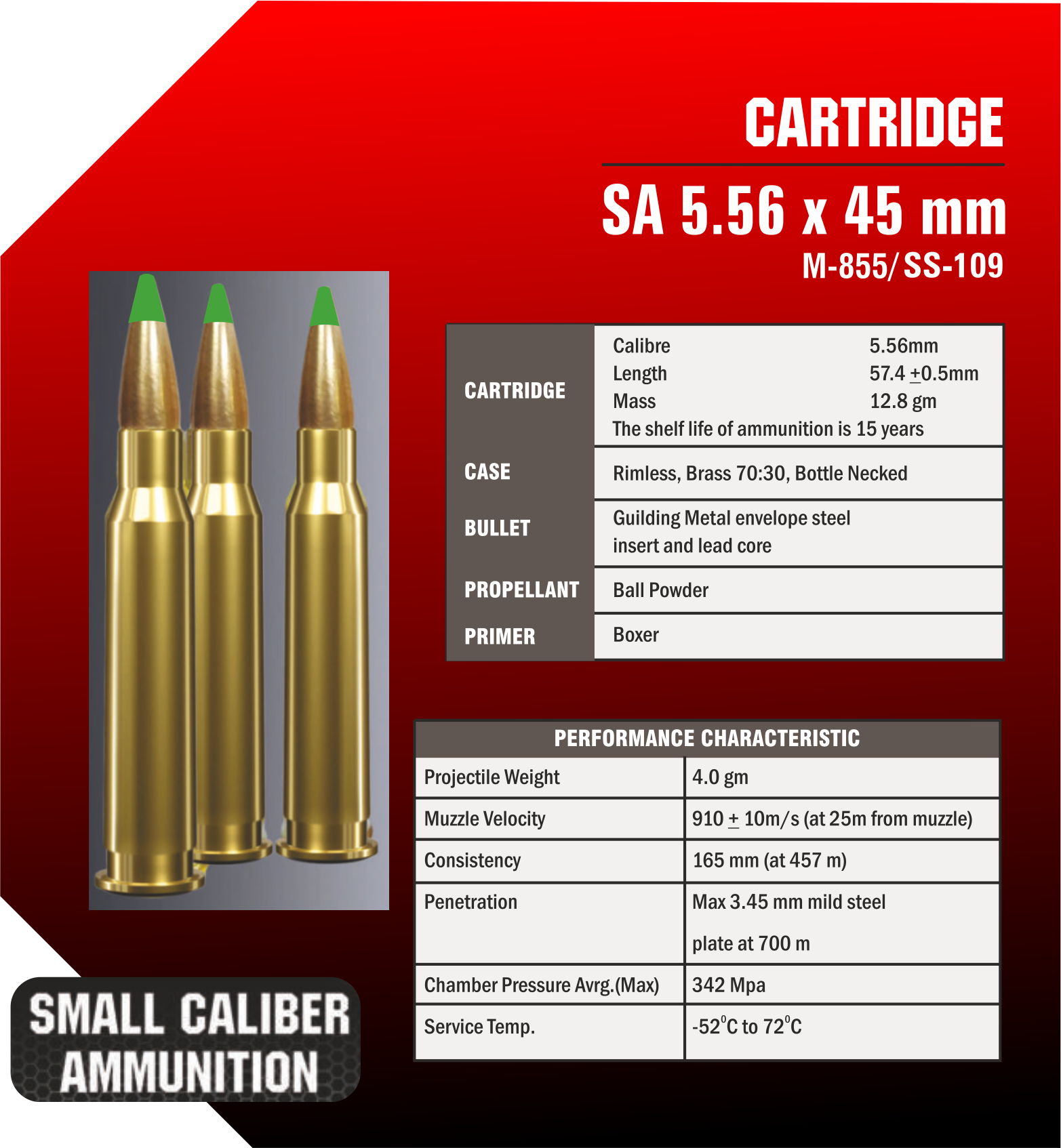
Manufacturing Process
Step 1: *Design and Engineering*
– *Technical Design*: Develop detailed designs and specifications for the 155 mm shell casings. This includes dimensions, material properties, and structural requirements.
– *CAD Modeling*: Use Computer-Aided Design (CAD) software to create detailed models and simulations of the casing.
Step 2: *Material Selection*
– *Raw Materials*: Choose high-quality metals such as brass or steel. The material must have the strength to withstand the stresses of firing and handling.
– *Material Testing*: Conduct tests on raw materials to ensure they meet the required standards for strength, ductility, and corrosion resistance.
Step 3: *Production Techniques*
– *Stamping/Forming*: Use stamping or forging techniques to shape the metal into the rough form of the shell casing. This step involves pressing the metal into a mold to create the initial shape.
– *Machining*: Precision machining is used to refine the casing to exact dimensions. This includes turning, drilling, and milling operations to achieve the required tolerances.
– *Heat Treatment*: Apply heat treatment processes to improve the mechanical properties of the metal, such as hardness and strength. Common treatments include annealing, quenching, and tempering.
Step 4: *Finishing and Quality Control*
– *Surface Treatment*: Apply surface treatments such as coating or plating to enhance corrosion resistance and durability. This might include processes like electroplating or painting.
– *Inspection*: Perform thorough inspections to ensure the casings meet all specifications and quality standards. This includes dimensional checks, material tests, and visual inspections.
– *Non-Destructive Testing (NDT)*: Use NDT methods such as ultrasonic testing or X-ray inspection to detect any internal defects or inconsistencies.
Step 5: *Packaging and Storage*
– *Packaging*: Package finished shell casings in protective materials to prevent damage during handling and transport. Use appropriate labeling and documentation.
– *Storage*: Store casings in a controlled environment to prevent corrosion or other forms of deterioration. Ensure proper inventory management and tracking.
3. *Technical Requirements*
– *Precision Engineering*: High precision in manufacturing to ensure casings fit correctly with other ammunition components and function reliably.
– *Material Strength*: Use materials with sufficient strength to withstand the pressures of firing and handling.
– *Quality Standards*: Adherence to military and industry standards for safety and performance.
4. *Regulatory and Compliance Considerations*
– *Military Specifications*: Ensure that the shell casings meet relevant military specifications and standards.
– *Export Controls*: Comply with export controls and regulations if manufacturing for international markets.
– *Environmental Regulations*: Adhere to environmental regulations related to manufacturing processes and waste management.
5. *Challenges and Solutions*
Challenges
– *Cost Management*: Managing the cost of raw materials and production processes while maintaining high quality. Explore cost-effective materials and production methods.
– *Supply Chain*: Ensuring a reliable supply chain for raw materials and components. Develop strong relationships with suppliers and consider diversifying sources.
– *Technical Complexity*: Addressing the technical complexities involved in achieving precise dimensions and high-strength properties.
Solutions
– *Advanced Technologies*: Invest in advanced manufacturing technologies and automation to improve efficiency and precision.
– *Process Optimization*: Continuously optimize production processes to reduce costs and improve quality.
– *Quality Control*: Implement rigorous quality control measures to ensure that all casings meet the required standards and specifications.
6. *Future Prospects*
– *Technological Advancements*: Embrace advancements in materials and manufacturing techniques to enhance the performance and cost-effectiveness of shell casings.
– *Growing Defense Markets*: Increased demand for artillery systems and ammunition presents opportunities for growth in the shell casing manufacturing sector.
– *Innovation*: Explore innovative designs and materials to meet evolving military requirements and improve competitiveness.
Conclusion
Manufacturing 155 mm shell casings involves a complex process that requires precision engineering, high-quality materials, and stringent quality control. By focusing on technological advancements, efficient production processes, and adherence to regulatory standards, manufacturers can produce reliable and high-performance shell casings that meet military requirements. Addressing challenges and exploring future opportunities will be key to achieving success in this sector.
Market Demand for 155 mm Shell Casings
Introduction
155 mm artillery shells are widely used in modern artillery systems and are critical for military operations. The demand for 155 mm shell casings is driven by defence modernization efforts, increasing artillery requirements, and geopolitical dynamics. This document outlines the market demand for 155 mm shell casings, including factors driving demand, key markets, and future prospects.
1. *Factors Driving Demand*
Defence Modernization
– *Artillery Upgrades*: Many countries are modernizing their artillery systems, leading to increased procurement of 155 mm shells and their casings.
– *Enhanced Capabilities*: Advances in artillery technology and the need for precision and extended range have boosted demand for high-quality shell casings.
Geopolitical Tensions
– *Regional Conflicts*: Rising geopolitical tensions and regional conflicts lead to increased defence spending and stockpiling of artillery ammunition.
– *Military Preparedness*: Nations are enhancing their military preparedness, resulting in higher demand for ammunition, including 155 mm shells.
Strategic Defense Initiatives
– *Indigenous Production*: Countries are focusing on indigenous production of defence equipment and ammunition to reduce reliance on imports and enhance self-reliance.-
*Export Opportunities*: Growing global demand for artillery ammunition presents export opportunities for manufacturers of 155 mm shell casings.
2. *Key Markets*
Domestic Market
– *India*: India has a significant demand for 155 mm shell casings due to its artillery modernization programs and defence needs. The Indian government’s focus on indigenous defence production under initiatives like “Make in India” further stimulates demand.
– *Other Major Markets*: Other countries with active artillery programs and defence modernization efforts also contribute to domestic demand.
International Market
– *NATO Countries*: NATO member countries, which standardize on 155 mm artillery systems, represent a substantial market for shell casings.
– *Middle East*: Countries in the Middle East with ongoing military conflicts and modernization efforts show high demand for artillery ammunition.
– *Asia-Pacific*: Nations in the Asia-Pacific region, particularly those with growing military capabilities, contribute to the international demand for 155 mm shell casings.
3. *Market Trends*
Technological Advancements
– *Enhanced Performance*: Advances in shell casing technology, including improvements in strength and precision, drive demand for more advanced casings.
– *Smart Ammunition*: Integration of smart technology into artillery shells increases the need for compatible and high-quality shell casings.
Increasing Production Capacities
– *Manufacturing Expansion*: Expansion of production facilities and capabilities to meet growing demand and improve supply chain efficiency.
Sustainability and Compliance
– *Environmental Regulations*: Adherence to environmental regulations and standards for ammunition production and disposal influences market dynamics.
4. *Challenges*
Supply Chain Constraints
– *Raw Material Costs*: Fluctuations in the cost of raw materials like steel and brass impact production costs and pricing of shell casings.-
*Logistics*: Efficient logistics and supply chain management are crucial for timely delivery and cost control.
Regulatory Compliance
– *Export Controls*: Adhering to international export controls and regulations can affect market access and operations.
– *Quality Standards*: Meeting stringent quality and performance standards is essential for maintaining market competitiveness.
5. *Future Prospects*
Growing Defence Budgets
– *Increased Spending*: Continued growth in defence budgets worldwide supports sustained demand for artillery ammunition and shell casings.
Technological Innovation
– *Advanced Casing Designs*: Development of advanced casing designs and materials to meet evolving military requirements and enhance performance.
Expanding Markets
– *New Markets*: Exploration of new markets and regions with emerging defence needs provides growth opportunities for manufacturers.
Conclusion
The market for 155 mm shell casings is robust, driven by defence modernization, geopolitical factors, and strategic defence initiatives. With increasing global demand and advancements in technology, manufacturers have significant opportunities to expand their market presence. Addressing challenges related to supply chain, regulatory compliance, and technological innovation will be key to capitalizing on these opportunities.